Online Induction >> Job Safety Analysis
Published 07/01/2025
Tips for Writing a Job Safety Analysis - Samples and Templates
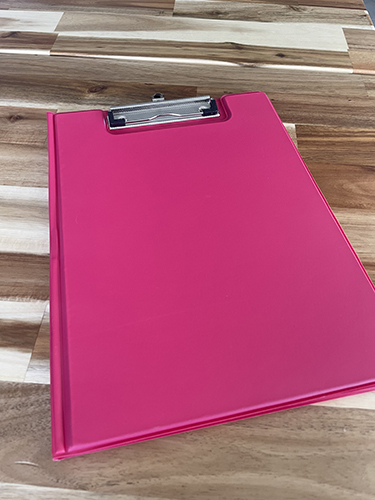
Job safety analysis is an approach that merges the accepted safety and health protocols into a particular job operation. All the steps in job safety analysis are meant to identify potential health hazards and the safety procedures of doing jobs. It was created to cater to employees' welfare while on duty. When all safety analysis measures are put in place, training and mentorship of workers are done effectively and efficiently. It is carried out at regular intervals.
A job safety analysis comprises of three main components, which include:
1: Tasks-Step by step lists of the primary activities of the work, for example, starting a machine.
2: Hazards-List of potential threats in every step of the tasks
3: Control measures-Instructions on how to perform the tasks safely while controlling every listed hazard.
A JSA might be collected as part of a
Contractor Induction,
Contractor Prequalification and part of your overall
contractor management system.
View JSA Templates, Forms and Examples
Here are the significant benefits of a job safety analysis:
By conducting a JSA, employers can identify potential hazards and risks associated with specific job tasks, allowing them to implement effective control measures to mitigate these risks. One of the significant benefits of a JSA is its ability to improve employee safety awareness and reduce the likelihood of workplace injuries. When employees are involved in the JSA process, they gain a better understanding of the potential hazards they may encounter while performing their job duties, leading to increased vigilance and proactive risk management. A thorough job safety analysis can enhance overall organizational efficiency by streamlining work processes and identifying opportunities for optimization. This structured approach not only promotes a safer work environment but also contributes to improved productivity and employee well-being.
- Aids in meeting safety protocols in the workplace
Since we work with manufactured tools and accidents are real, a JSA guarantees total safety for workers. Workers find it easy to work when they are assured that there are laid protocols that will take care of them in the event of an accident.
A JSA ensures the company follows the government and health department laws regarding employees' safety. Also, JSA will differ from one job to another depending on which machinery is used and the industry the company is operating in. For example, an electrical company will have a different JSA from a chemical company.
- Reduce accidents
A JSA gives detailed instructions on how to perform a specific job, and by reading it, employees become aware of how to operate the machines. Work is done with little or no accidents. The workers' output is enhanced as a result of the implementation of safety measures within the company.
- Provides a training guideline
Training of new employees involves a lot of try and error, and so trainees are exposed to accidents while handling tools. Even after training, new employees take time to learn the company's culture and become familiar with the tools.
A JSA provides a guideline on how training is conducted and how to handle different devices. With JSA knowledge, every trainee can minimize injuries since they already have awareness.
- Improves communication
Designing a JSA requires information from different sectors in the company, and so communication is improved. Employees at all levels are requested to give their views after reading the JSA; their input is used to rectify areas that do not fit their safety.
Since their ideas are discussed in an open meeting without intimidation, they feel free to interact with their top managers and give unbiased information. By such interaction, non-documented safety issues are discovered and put into consideration.
Some examples of JSA for different industries include:
- Construction
- Electrical
- Excavation
- Generic
- Daily
See more with:
What is a JSA? and Why is it important?
How to write a Job Safety Analysis: The Guide
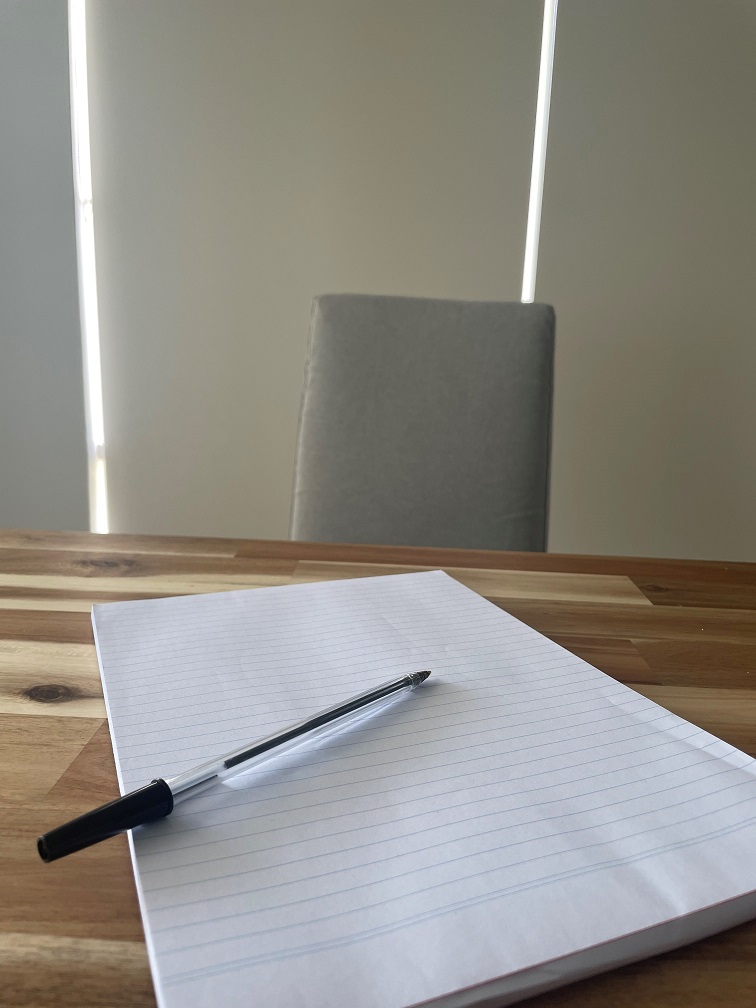
1: Select the job
To start a JSA, choose which job to analyze and determine all possible health hazards associated with the job at hand. Selecting which job to analyze is not an easy task, and you should prioritize with the one with the highest probability of accidents or illness.
Challenging jobs and the ones with high chances of errors and must be given priority. When implementing a new job or equipment that requires new instructions, it is good to carry out a JSA as soon as possible. The JSA should contain accurate information on the dangers workers are exposed to while on duty.
2: Breakdown the job
Each job under analysis must be broken down into processes that must not exceed ten. The procedures should be addressed so that they appear to solve the health hazards and safety issues in the order that employees are likely to face them. The breakdown should be carried by a professional or a competent supervisor who watches the job as a proficient employee performs it and record the processes.
3: Identify the hazards
Hazards should be identified as soon as the observation and recording are over. In the identification process, the interaction of the employee and the machinery is noted down, possible falling or slip of the machinery while in operation, and potential exposure to extreme pressure or heat. Other risks which should be noted are; coldness, excessive noise, vibration, toxic radiations, and fumes.
4: Determine preventive measure
This is the final stage and the most vital. What benefit will it be if the analysis is done and no measures are put in place? All potential health hazards are eliminated in this stage, processes modified, and machines changed if possible.
In such a case where the dangers cannot be avoided, machine guards are used to safeguarding the workers, and risk allowances are given. Reasonable steps are added while dropping unnecessary steps. Employees' morale is enhanced if they are working in an environmentally conducive environment, and it is met through quality job safety analysis.
Make JSA's Easy with QR codes and Mobile Responsive
Try setting up your JSA's on mobile or enable easy completion via QR codes or with mobile live links. Using these modern mobile tools, you can ensure contractors and staff have quick easy ways to access and complete JSAs
- Create QR code posters
- Issue a mobile link to a JSA form
- Create mobile responsive JSA forms
Try turning your JSA form into a mobile responsive form or generate a QR code poster
Sample JSA: An example Job Safety Analysis Template
Use our ready to go JSA Temlate
What are some examples when you would need a JSA?
Commonly it might be for situations such as:
- A job task has a potential risk of resulting in an injury or incident in the workplace
- The job task has had a previous occurrence of an incident or near miss in the workplace
- Jobs that involve multiple steps or repetitive motions or perhaps carried out in a new environment
- It could be a job task or activity rarely implemented by the workers implementing them
- As part of a
Permit to Work
- Extreme or high risk work tasks
A Job Safety Analysis is important to manage before contractors are working on site because it helps ensure that all contractors are following safe working practices and that the job site is safe for everyone. It also helps identify any potential hazards and how to address them, as well as any safety measures that need to be taken before and during the job. By managing Job Safety Analysis before contractors are working on site, it helps reduce the risk of accidents, injuries, and fatalities.
If a Job Safety Analysis is not checked before contractors are working on site, there is a risk that they may not be aware of the potential hazards associated with the job they are undertaking. This could lead to accidents or injuries, and could potentially put the contractor and other workers in danger. Additionally, not checking a Job Safety Analysis could result in costly fines or penalties from regulatory authorities, as well as a potential lawsuit if an injury does occur.
Use Case: JSA in Construction
A job safety analysis is an important tool used in the construction industry to ensure the safe performance of tasks.
It is a procedure that helps to identify potential hazards and develop safe work practices and procedures to mitigate those risks. JSA is a systematic method used to identify hazards and determine the best way to eliminate or control the hazard.
It requires an analysis of each job step, an identification of the associated hazards, and an evaluation of the potential risks.
The JSA process is used to develop an action plan to address hazards, assess the effectiveness of existing controls, and provide guidance for implementation of new controls.
Ultimately, the goal is to reduce or eliminate the risk of injury or illness to workers. The JSA process helps to ensure that all workers involved in a job understand the tasks, the associated risks, and the necessary safety measures to be taken.
Job Safety Analysis Frequently Asked Questions
When would you need a JSA?
This type of tool takes into account potential hazards that could arise from doing particular jobs and makes sure the right precautionary steps are taken to ensure the safety of workers. In other words, it's a detailed assessment of different processes or tasks which helps protect individuals from anything that could potentially be hazardous. But when would you need a JSA?
A JSA can prove vital for any work environment where there might be risks involved in day-to-day activities such as handling chemicals and machinery or even simply carrying out general maintenance tasks. The analysis allows employers to clearly identify dangers, analyze them properly so they can come up with preventive measures instead of reacting after an accident has already happened
How often would you complete a JSA?
It depends on your particular industry, work environment and hazards present in it. For industries with transforming or changing operations frequently such as construction sites or marine vessels, organisations should conduct JSAs regularly, usually daily. Other work sites which have detailed processes yet tend not show significant changes may only require less frequent but scheduled JSA audits. Usually this will include things like quarterly - bi-annual reviews of tasks and working conditions identified during the initial risk assessments process; however review schedules are flexible based on individual organisation requirements, from weekly shifts through to step back reviews every six months.
Where can I view a JSA template or build a JSA workflow?
Right here!
How do you conduct a Job Safety Analysis?
It is important to familiarize yourself with the material that needs to be examined in order to properly detail any potential risks or hazards associated with any given task. Researching training manuals, observing current processes and procedures are all helpful when gathering information on what constitutes a safe working environment for every worker involved. After gaining some insight into each particular process, suitable corrective actions can then begin to take shape as far as stopping hazardous occurrences from happening in the first place.
When conducting workplace assessments for a proper job safety analysis all aspects should be considered--from physical attributes such as lighting requirements down to equipment design elements like shielding obstructive operators view windows which may hinder visibility when attempting certain tasks efficiently or within regulatory guidelines set forth by applicable industry governing bodies.
Try creating and managing JSA's using our online JSA Manager