Online Induction >> How to write the best Safe Work Method Statement (SWMS)
Published 04/06/2023
How to write the best Safe Work Method Statement (SWMS) for 2024
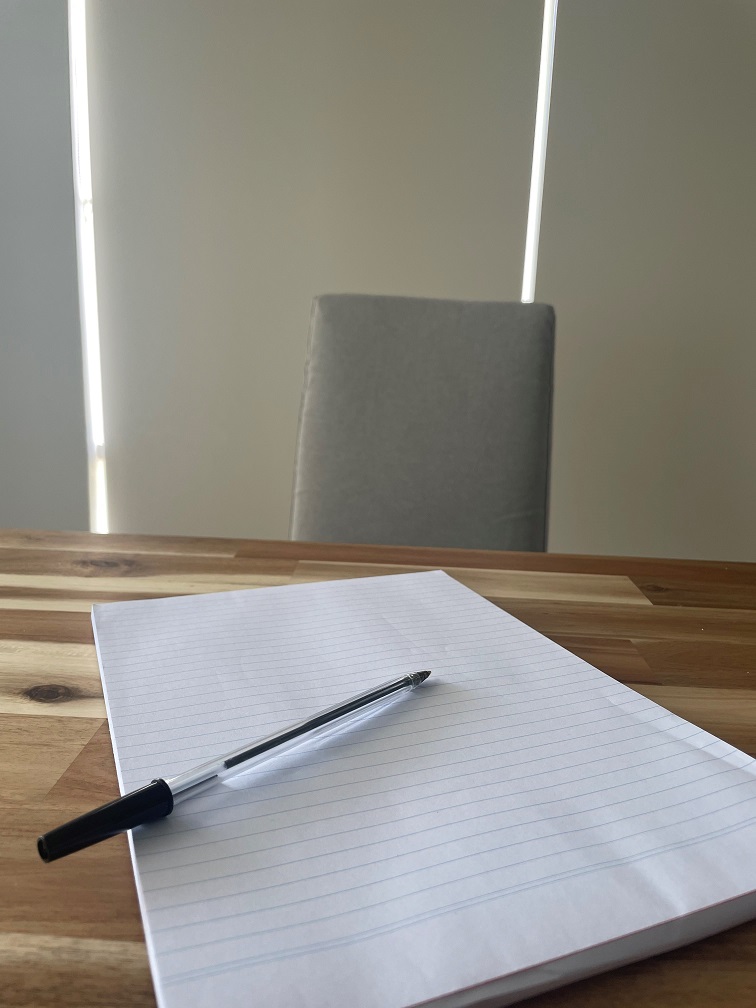
Risks in the workplace are inevitable, but that does not necessarily mean people should not engage in risky activities while prosecuting their tasks. However, some are so risky that they should be avoided at all costs unless there are well-laid protocols for combating misfortunes when they happen.
While we cannot predict when incidents, near misses, hazards, injuries, and accidents happen, it is good enough to have mitigation and recovery measures. Companies and self-employed people should have protocols for eliminating misfortunes when they happen. How can it be done to ensure employees are safe and healthy in workplaces?
It is through the implementation of safe work methods. All incidents, hazards, accidents, near misses, and injuries must be recorded when they happen, the possible ways of mitigating them, the factors that led to the occurrence, and the medical procedures taken.
This information helps in designing the
Safe Work Method Statement. Well, what is a safe work method statement? It is a healthy and safety planning tool to identify risks, hazards, near misses, and incidents. It records them to find control measures for mitigating them.
An effective, safe work method statement should explain how risks will be controlled to ensure a healthy and safe work environment.
An SWMS should identify tasks with a high probability of risks, hazards involved, describe control measures, and how the control steps are to be implemented. Some of the high-risk working environments that require a safe work method statement include; construction, chemical plants, electrical wiring, critical systems like airplanes and ships.
Ideally, a safe work method statement should be short and precise, describing the hazards in understandable language and the mitigation measures. While many employers may confuse what to include in a safe work method statement, training, manuals, and work procedures should not be included. A safe work method statement is prepared by the employer and implemented by the employees.
Some standard safe work practices include; isolating people from a hazard like fencing a chemical treatment chamber, substituting lower risk activities, implementing hazard control laws, and utilizing engineering controls.
A Safe Work Method Statement is usually collected and checked as part of a
contractor induction or
contractor prequalification.
This will form part of your overall
contractor management system and
contractor compliance. It may also be checked as part of a
contractor sign in system.
Discover our SWMS Management Platform
Components of a safe work method statement
A method statement should include the following information about any task.
- The project
The project to be undertaken should be highlighted in the safe work method statement. The project information includes; the main contractor, sub-contractors, employer, the number of employees to be included, list of processes to be included, and duration.
- Specific activity
All activities have different safe work method statements. An example is the method statement for roofing should be unique from painting. Every activity should be described in detail, the nature of tools to be used, and height from the ground level.
- Work description
The specific work is described in this section. The departments to be included in the job are defined, supervisors for all departments, the number of employees allocated to each supervisor, the exact location of the job, and any relevant information.
- Duration of the task
The time allocated for the job and the specific tasks are defined here. The start and end times for the tasks should also be defined. By defining the total time allocated, it is possible to plan for the resources required to finance mitigation measures.
- Risk identification
The primary purpose of the safe work method statement is the identification of risks in the workplace. It identifies high-risk tasks, processes, or environments which can cause harm to employees. In the risk identification, construction is considered the activity with a high probability of risks, thus the name High-Risk Construction Work (HRCW). The HRCW is contained in the safe work method statement. The HRCW contains eighteen high-risk activities that help identify risky activities.
- PPEs requirements
Safety measures start with wearing protective gear. The method statement should include specifications of the PPEs required by each task. Taking construction as an example, the PPEs required by masons is different from a carpenter - also, the exact location for fire extinguishers, first aid kit, water, and first-aid specialist.
- Welfare arrangement
Employees need to know what measures the company will take when an employee is injured while on duty. The employer should have plans to compensate employees who get an accident and pay them while home for recovery, medical care, and special attention to victims.
- Emergency procedures
Employees want to know which emergency measures the employer has put in place. The employer should have an emergency response team to address misfortunes when a specific hospital admits injured employees.
Benefits of a safe work method statement
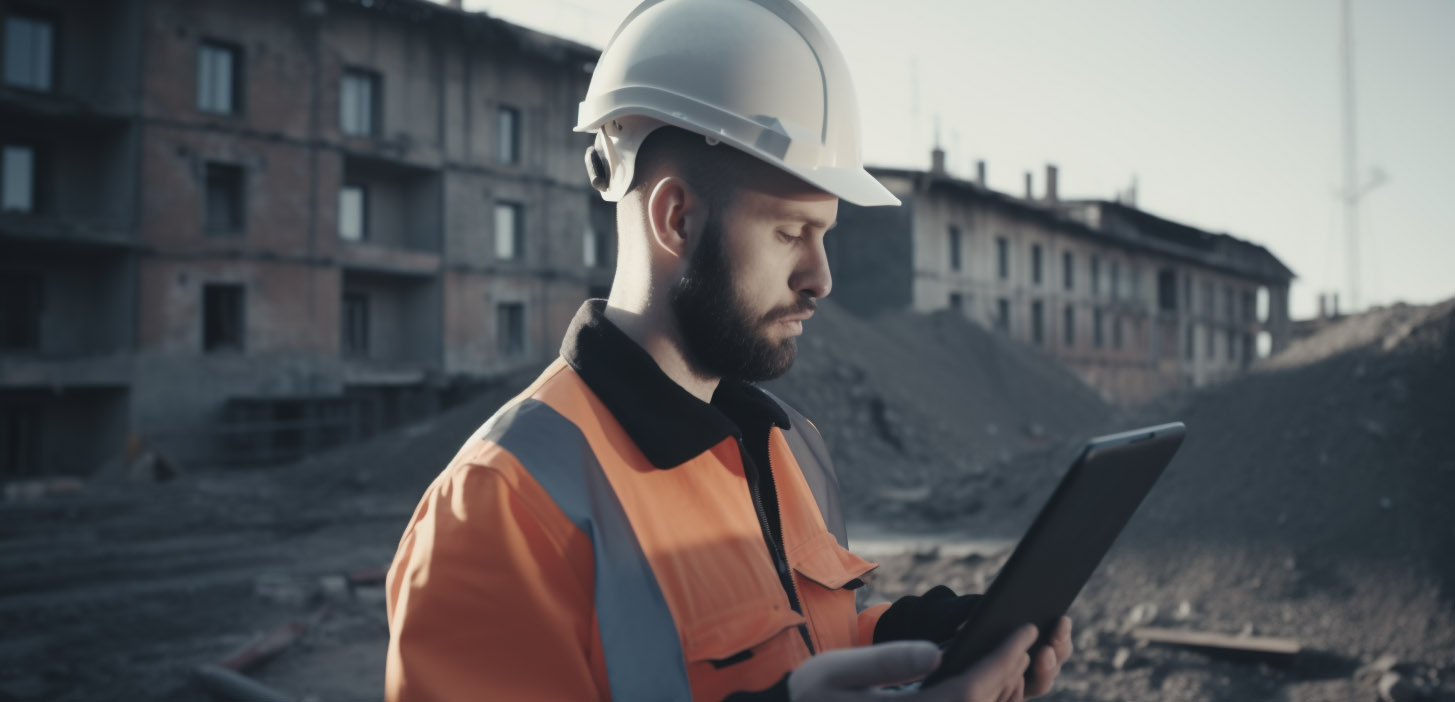
Employers create safe work methods purposely to comply with legal requirements for health and safety. Although they are solely designed for legal requirements, they serve a purpose in promoting healthy living and the progress of the business. Here are the benefits of implementing a safe work method statement.
- Comply with the legal requirements
It is a legal requirement for employers to provide safe and healthy living for employees. The law demands that every employer have measures to mitigate risks and recover from accidents. As per the law, when employees are injured while on duty, the employer should be held accountable and ensure the victims undergo treatment, receive compensation, and receive monthly salaries even as they recover.
- Client requirement
Since outsourcing is becoming a trend, companies are finding themselves at the receiving end. Clients demand health and safety protocols before outsourcing tasks to other companies. Since the outsourced company works from the client's premises and interacts with the client's employees, the client company needs to know protective measures before outsourcing the task.
- Helps in planning the work
It is good enough to establish what process or tool can harm employees other than learning from mistakes before starting any task. It is not a catchy saying that if you fail to plan for safety, you will be planning for safety failure, but it is true, anyway. When the possible hazards are known, it is easy to plan for work and the required resources to finance preventive measures.
- Lays out preventive measures
It is easier to put control measures when writing the method statement than when the job has kicked on. Resources are budgeted and the best mitigation measures vetted during the planning stage. Again, laying down the measures before commencing eliminates delays when implementing the measures in the field.
- Facilitates better decision-making
Decisions implemented on the table are sound as compared to field decisions. Generally, brainstorming ideas and coming up with the best options at the planning stage yields sound decisions. When the preventive measures are written prior to implementation, it is possible to prioritize them.
- Serves as a communication channel
Written communication has benefits over verbal communication. When employees are given the method statement, they adhere to the protocols as required. Writing the method statement eliminates communication barriers, misunderstanding, and misinterpretation of information.
- It's a monitoring tool for health and safety.
Implementing the method statement document is not enough; it should be monitored to establish whether health and safety are maintained as planned. The feedback received from the employees is used to identify strengths and weaknesses in the preventive measures. The effectiveness of the document is established when feedback is given.
View SWMS Templates, Forms and Examples
Checklist for writing a safe work method statement (SWMS)

1. Does the SWMS contain company name, address, and contact information?
2. Does the SWMS include project information, i.e., Site address and job description?
3. Is there evidence on the SWMS that shows the team that developed and implemented it?
4. Is there information about the principal contractor and the date the method statement was provided?
5. Does it identify high-risk work?
6. Does it include current legislation, code of ethics, and standards?
7. Does the SWMS include emergency procedures?
8. Does the SWMS template include site information, equipment and tools, processes, and harmful substances required in the task?
9. Does the SWMS list inspection and maintenance measures for the equipment and tools to use?
10. Does the SWMS include hazards, risks, and mitigation measures for completing the job?
11. Does the SWMS template include PPEs?
12. Does the SWMS have proof of appropriate license, qualifications, and training for undertaking the job?
13. Does the SWMS include a section for recording development, approval, and review date?
14. Does the SWMS include risks for each particular task?
This is a typical example of an SWMS and its implementation.
A contractor wins a job to install electric wiring in a newly built apartment; it is known there will be a risk of engineers falling more than three meters (HRCW), so SWMS will be needed. The contractor meets the workers to consult on the way forward.
The workers suggest the following;
- The wiring on the walls be completed before plastering to minimize plumbing tasks, therefore partially eliminating the risk of falls when climbing a ladder and digging the walls. However, the falling risk remains.
- Where wiring cannot be done before plastering, a scaffold can be used to climb the wall, but only light electricians will install the wiring. The risks will have reduced by using lighter people who can be supported by the scaffold.
- A risk remains that an electrician can fall from a height of three meters if the scaffold is wrong placed on the ground or the electrician sways.
- The risk will be reduced further when the electricians are trained on using the scaffold, possible hazards identified, and warnings posted on risky areas.
We cannot avoid unavoidable incidents in the workplace but can be minimized through the use of a safe work method statement. When implemented, it is possible to reduce staff turnover absenteeism, increase return on investment (ROI), and increase efficiency.
Try creating your own safe work method statement process here:
See how our online management of (SWMS) safe work method statements for contractors can work for your organisation